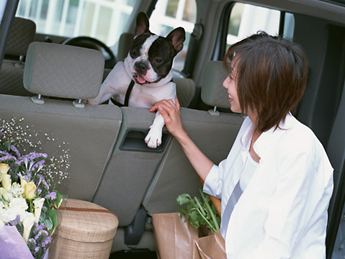
Japanese automobiles are becoming more and more high-performing and fuel-efficient. They're also increasingly earth-friendly, and the average driving experience is even more comfortable. Our resin is used in the production lines of world-famous Japanese cars.
Resin plays an important supporting role essential in the manufacturing of car partsh
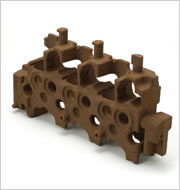
Resin is now an essential material for automotive manufacturing. Although it is not used for the parts themselves, it has its uses in the manufacturing process for chassis parts such as engines and brakes, as well as portions of the exhaust system. This process is called "casting". The molten alloy (such as aluminum and iron) is poured into a mold and solidified to make each part (casting). This is the chief method of manufacturing auto parts, since a complex shape can be created using only one mold. There are a few casting methods; our manufacture a shell mold resin used in sand casting. Casting using a sand mold involves sand hardened by a binder and formed into a strong mold. Shell mold resin is a type of binder that acts as an adhesive, gluing sand particles together for hardening. We also manufacture resin-coated sand, in which sand is precoated with resin. Furthermore, we perform research and development on binders and resin-coated sand in response to our customers' needs.
Resin-coated sand that becomes a material for molds
The casting process is shown in the chart below. We provide the shell mold resin and RCS (resin-coated sand) used in (1) below, and recycles the sand collected in (6).
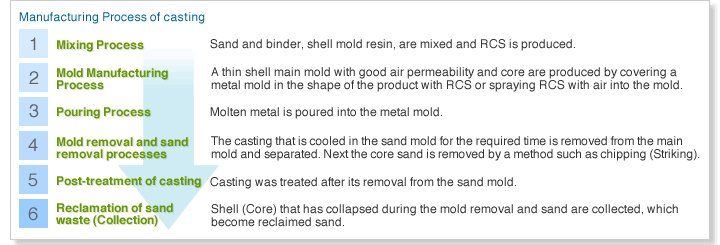
Great contribution to the high performance of cars
Japanese cars have become top-class vehicles worldwide. We have contributed greatly to the progress of the automotive industry from behind the scenes. Due to the development of various types of RCS, complex molded shapes can now be mass-produced, contributing greatly to high automotive performance. We have come up with an improved tar-reducing RCS exclusively for aluminum, suitable for casting at low temperatures. We have succeeded in both the vast reduction of tar adherence to the metal mold and in obtaining outstanding collapsibility. Productivity has skyrocketed thanks to these new materials, which have helped make automotive parts increasingly lightweight. Our shell mold resin and RCS have played a role in the high performance and decreasing weights of today's automobiles.
Recycling since 30 years ago
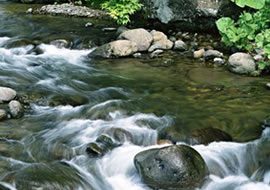
We have been active in recycling for thirty years. Sand used in casting is collected, heated into a fluid, and is reused as "reclaimed sand", a component in RCS. We contribute to the reduction of waste matter and the saving of resources. In addition, we developed a low-formaldehyde resin that reduces formaldehyde output. This resin has helped us reduce the production of formaldehyde by 50 percent compared to conventional novolac resins. Offensive odors have been a side effect of the process that made it possible to lower the temperature of metal molds. We successfully developed a monomer-free resin to reduce the source of offensive odors emitted from the entire factory, and a "fruity resin" that results in a fruitlike scent during molding. These new materials have become useful in improving the environment both within factories and in their vicinities by effectively reducing offensive odors during manufacturing. We will continue to strive to develop products and equipment with consideration for the environment.
Sand products for casting
Our product lineup of resin-coated sand and aggregates used in sand casting molds.
Click here for resin product information